Witajcie w nowym 2013 roku.
Jako, że sezon zbliża się z każdym dniem czas na testy pianki poliuretanowej (wlewowej).
Jeszcze w zeszłym roku (jak to brzmi:) zamówiłem piankę EKO PRODUR PM 4032 firmy Progmar.
Przesyłka dotarła bezpiecznie i dzisiaj rano ją odebrałem.
Jak się domyślacie prawie natychmiast rozpocząłem testy a wyniki i dokumentacja foto poniżej.
Tytułem wstępuZgodnie z tym co pisałem wcześniej planuję co 50 cm wlaminować cienki (szerokości 10-15 mm) pas sklejki (grubości 6-8 mm). Do tych pasów w kolejnym etapie remontu będą przymocowane arkusze sklejki (wraz z matą korkową, w górnej połowie ścian oraz na suficie). Przestrzeń pomiędzy skorupą a w/w arkuszami nie może zostać pozostawiona pusta. Konieczne jest jej wypełnienie. Możliwości jest wiele - począwszy od steropianu, wełny mineralnej, filcu, macie zagrzejnikowej itp. Ja postanowiłem przetestować pianki poliuretanowe. Technologia natryskowa w takiej małej przestrzeni się nie sprawdzi a i ograniczenia technologicznie nie pozwalają na nałożenie bardzo cienkiej 5-8 mm warstwy. Poszukałem w sieci i znalazłem pianki wlewowe, dwuskładnikowe, które po zmieszaniu 2 komponentów nanosi się ręcznie.
PiankaJak już wspomniałem do testów użyłem pianki EKO PRODUR PM 4032 firmy Progmar.
http://www.progmar.waw.pl/produr-4032-p-75.html
Środowisko testoweJak się domyślacie, nie miałem zamiaru testować pianki na żywym organizmie (tzn mojej N132), zatem stworzyłem namiastkę oryginału.
Wykorzystałem stare drzwi szafowe (o szerokości 50 cm), do których przykręciłem listwy sklejki grubości 12 mm. Całość uzyskanej przestrzeni została zakryta płytą z plexi, co miało ograniczyć rozprzestrzenianie pianki oraz pozwalało naocznie obserwować przebieg testu (głównie potencjalne ryzyko "wypchania" przez rozszerzającą się piankę ścian - każdy chyba ma mniej lub bardziej złe wspomnienia z piankami montażowymi).
Warunki laboratoryjne testuJak zapewne wiecie, wszelkiego rodzaju pianki, żywice, itp sztuczne, dwuskładnikowe lub wieloskładnikowe produkty wymagają ciepła i małej wilgotności otoczenia. Moje testy rozpocząłem w garażu, przy temp. +3 st. C o wilgotności mocno przekraczającej zalecenia producenta ... ale co tam. Musiałem się przekonać na własne oczy jak będzie.
Rozpocząłem od testu samej pianki czyli dokładnie wymieszałem po 5 ml obu składników a następnie uzyskaną mieszankę wlałem do starego opakowania po cafe latte by Grycan. Na kolejnych fotkach efekt polimeryzacji składników...
MetodykaZaplanowałem 2 metody wypełniania nieszczęsnej wolnej przestrzeni:
A) poprzez nawiercenie otworów w plexi i podania strzykawką wymieszanej pianki
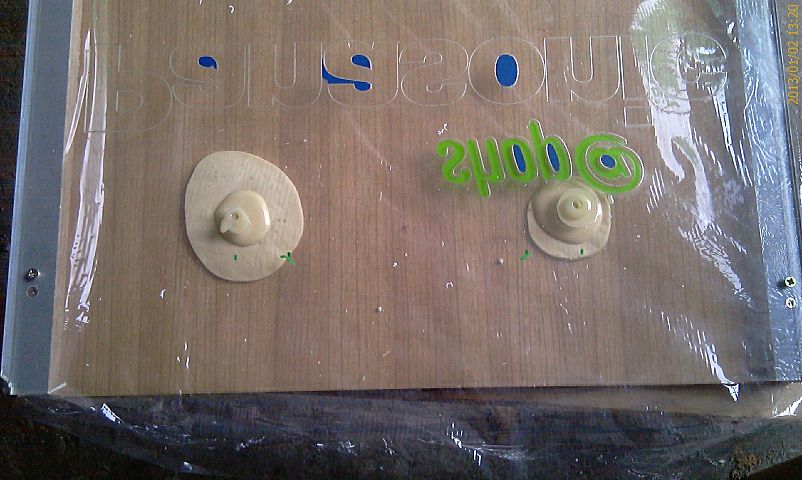
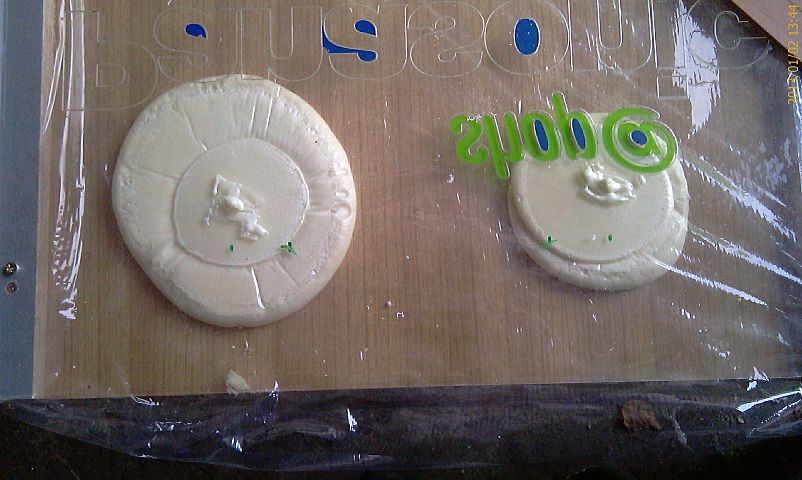
B) poprzez naniesienie na 10 cm pas testowy, warstwy pianki o grubości 1 mm a następnie przykręcenie plexi
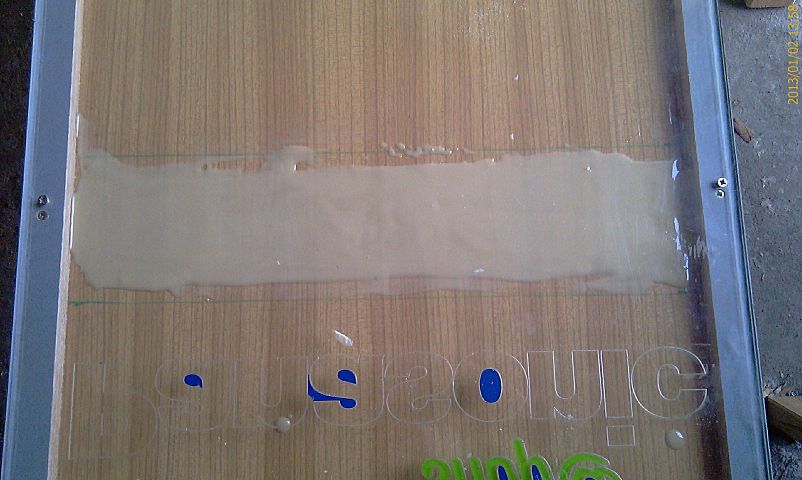
Wyniki i wnioskiZ podanych wyżej metod wydaje się, że metoda B jest lepsza. Podając odpowiednią warstwę pianki, po spolimeryzowaniu uzyskujemy pełne wypełnienie naszej pustej przestrzeni. W moim teście warstwa 1 mm grubości pianki była zbyt mała do uzyskania wypełnienia w 100%, ale proszę wziąć pod uwagę, że to pierwsza faza testów i nie miałem pojęcia czego się spodziewać.
Metoda A nie jest w pełni satysfakcjonująca ponieważ, jak widać na zdjęciach, pozostają puste, niewypełnione przestrzenie - zatem nie osiągnęliśmy zamierzonego celu.
Pozostaje jeszcze jedna bardzo ważna kwestia do omówienia.
Otóż zalecenia producenta dotyczące warunków wykorzystania pianki są niezwykle istotne. Pomimo niskiej temperatury i dużej wilgotności pianka polimeruje ale... uzyskana pianka jest bardzo nietrwała i krucha. Można ją w palcach rozkruszyć uzyskując prawie pył.
Z uwagi na powyższe powtórzyłem test B w warunkach domowych czyli niska wilgotność, temperatura otoczenia 20 st. C, temperatura komponentów 25 st. C. Zgodnie z oczekiwaniami uzyskany produkt był w 100% zadowalający. Pianka o bardzo dużej twardości i odporności mechanicznej, bez żadnej kruchości. Sam proces polimeryzacji o wiele szybszy i bardziej efektywny. Na zdjęciach możecie zobaczyć porównanie
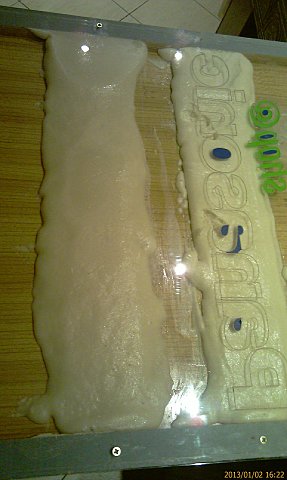
PodsumowanieWydaje się, że wykorzystanie pianki poliuretanowej jest trafionym pomysłem. Odpada konieczność dokładnego szlifowania powierzchni skorupy, uzyskane wypełnienie jest pełne i dokładne, bez żadnych spoin i mostków termicznych. Zastosowanie zamkniętokomorowej pianki niweluje wpływ zmian temp (i ciśnienia) na ew. skraplanie się pary wodnej między skorupą a warstwą wewnętrzną. Uzyskana pianka jest hydrofobowa, doskonale izoluje termicznie i akustycznie, choć z uwagi na małą grubość warstwy na cuda bym nie liczył.
I co dalej....Jak się domyślacie to nie koniec testów...
Zamówiłem dzisiaj kolejny produkt a mianowicie EKO PROFLEX 140 czyli dwukomponentowy systemem poliuretanowy do
produkcji pianki elastycznej formowej o podwyższonej gęstości i wytrzymałości mechanicznej.
Wydaje się, że będzie jeszcze lepiej spełniała moje wymagania... Posiada zalety pianki testowanej powyżej + jest w pełni elastyczna. Co jest bardzo istotne podczas jazdy, kiedy budka pracuje.


Wyniki testów wkrótce.....